ADHESIVE MORTAR
KLM-20W is an element of the external thermal insulation composite system with plaster (ETICS) marketed under the trade name KLEIB.
- high yield
- easily workable
- white
- fibre reinforced
- increased adhesion and very high degree of resilience
- for white and graphite styrofoam
- for forming imitation of the façade cladding board
- does not contain lime.
INSTRUCTIONAL VIDEO:
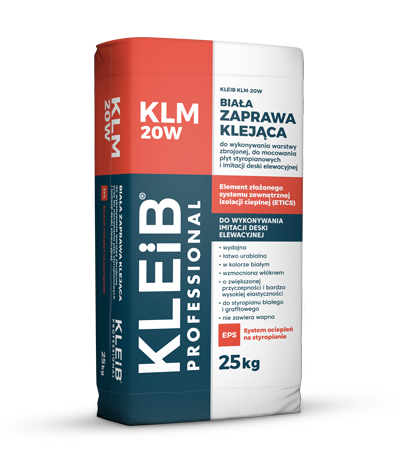
25 kg
54
Approx. 3.0-4.0 kg/m2 for forming a reinforced layer.
Approx. 4.0-5.0 kg/m2 for attaching boards.
KLM-20W is a white cement adhesive mortar for forming a reinforced layer in the KLEIB system. It is also suitable for fixing styrofoam panels on all typical, structurally sound and even mineral substrates (concretes, plasters, brickwork, hollow blockwork, stone elements, etc.). It can be used to imitate a façad cladding board structure using an imprint mould.
Before the formation of a reinforced layer, the surface of the styrofoam boards should be even, clean, stable and free of dust where the boards were grinded after adhesion. In case of using mortar to attach styrofoam boards, the working surface should be stable, even and structurally sound i.e. strong enough, free from layers that may weaken mortar adhesion, in particular dust, dirt, lime, oil, grease, wax, or residues of oil and emulsion paints. If the surface is too absorbent, it should be primed. For these works it is best to apply KLEIB G1 primer.
The mortar is prepared by pouring the entire contents of the bag into a container with a measured amount of water and mixing until a smooth, lump-free uniform consistency is obtained. The mortar is ready to use after 5 minutes and after remixing. Prepare portions that are to be used within approx. 2 hours.
For bonding styrofoam boards on even surfaces, it is advisable to apply the mortar on the entire surface of the insulation boards and spread it with a notched plasterer’s float. In case of an uneven working surface, the mortar should be applied to the board in the form of thick layers along its edges, at the distance of approx. 5 cm from the edge, along with 3 to 6 patches of mortar uniformly distributed on the rest of the board’s surface. As a result a min. 60% of the surface must be sufficiently adhered to the working surface. Vertical connection of the boards should be maintained in a staggered arrangement. Further work, i.e. any use of suitable fasteners, grinding of uneven surfaces of boards, or the application of a reinforced layer can be performed no earlier than after 72 hours. In order to add a reinforced layer on the surface of adhered styrofoam boards one should apply mortar with the minimum thickness of 3 mm, spread it with a notched plasterer’s float and embed in this a reinforcing mesh of fibreglass. The mesh is best embedded in an arrangement of vertical strips and these to be smoothed so that it is completely invisible and at the same time is not in direct contact with styrofoam boards. The mesh should be firmly stretched out and completely covered with a layer of mortar with the minimum thickness of 1 mm. Mesh strips should be connected to each other by a min. 10 cm wide overlap. Priming with a suitable primer can begin no earlier than after 72 hours. In order to obtain an imitation of the board structure, apply adhesive mortar evenly on the substrate with the thickness of about 3-5 mm. Then apply the release agent to the silicone mould and press the desired pattern. After mortar setting (approx. 3 days), the surface can be painted with a tinted AF-10 product in the selected wood colour. The use of protective nets on scaffolding is recommended for all works. Tools should be washed with water immediately after use.
Approx. 3.0-4.0 kg/m2 for forming a reinforced layer. Approx. 4.0-5.0 kg/m2 for attaching boards.
The mortar must be transported and stored in tightly sealed bags, in dry conditions. Protect from dampness. Shelf life in conditions that comply with the specified requirements is 12 months from the production date on the packaging.